Packaging Equipment Service: Prolonging the Life of Your Machinery
Packaging Equipment Service: Prolonging the Life of Your Machinery
Blog Article
Professional Product Packaging Equipment Service for Seamless Procedures
In today's fast-paced manufacturing atmospheres, the importance of expert packaging devices service can not be downplayed. Such services not just enhance operational performance but additionally play an important function in minimizing downtime and making sure product high quality. By leveraging proficient technicians for precautionary maintenance and timely repairs, services can browse the complexities of equipment management (packaging equipment service). The landscape of devices service is evolving, offering both obstacles and opportunities that require further exploration. What variables should companies think about when buying these important services to secure their one-upmanship?
Importance of Specialist Service
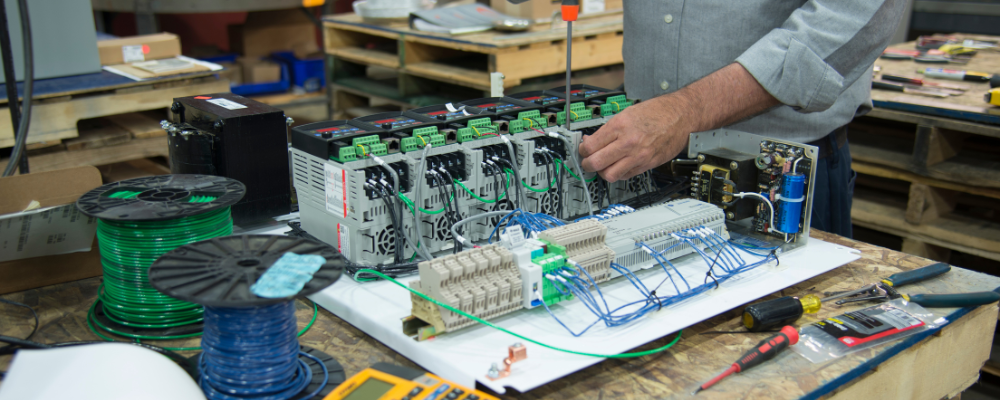
Furthermore, regular servicing by professionals aids prolong the life expectancy of product packaging equipment. Expert solution carriers are outfitted with thorough knowledge of different equipment types and market standards, enabling them to execute preventative upkeep successfully. This proactive technique not only lowers the possibility of unforeseen failures however additionally boosts general functional dependability.
Additionally, professional solution can considerably contribute to compliance with regulatory criteria. Packaging tools need to follow strict security and high quality standards, and specialist technicians make certain that these criteria are met continually. This not just safeguards item integrity yet additionally shields the business's track record.

Benefits of Expert Support
Involving professional support for product packaging devices not only enhances functional effectiveness but additionally provides a range of added benefits that can substantially impact an organization's profits. One of one of the most noteworthy benefits is the reduction of downtime. Expert specialists can quickly identify and settle issues, guaranteeing that assembly line stay active and minimizing the financial losses connected with idle machinery.
In addition, professional support often consists of preventative upkeep, which can prolong the lifespan of product packaging tools. By frequently servicing machinery, possible troubles can be identified and dealt with prior to they intensify into expensive repair work or substitutes. This proactive method not only saves money however additionally improves item high quality by ensuring that tools operates within optimal specifications.
In addition, leveraging the proficiency of skilled professionals can result in boosted conformity with sector regulations. These professionals stay updated on the most recent standards and can guide organizations in executing ideal methods, consequently staying clear of prospective lawful responsibilities.
Types of Product Packaging Devices Solutions
When it involves packaging devices services, organizations can pick from a range of options tailored to satisfy their specific demands. These services generally come under several classifications, each created to enhance functional efficiency and lessen downtime.
Preventive upkeep solutions concentrate on regular assessments and upkeep tasks to ensure that devices operates smoothly and decreases the chance of unexpected break downs. This Extra resources aggressive approach can expand the life expectancy of equipment and boost efficiency.
Repair solutions are important for attending to tools malfunctions or failures - packaging equipment service. Skilled service technicians detect the issues and do necessary repairs, making certain that the equipment is recovered to optimum working conditions immediately
Setup services are crucial when presenting new product packaging devices. Experts take care of the setup, guaranteeing that the equipment is incorporated correctly into existing lines and functions as meant.
Educating services offer personnel with the essential skills and knowledge to operate equipment successfully. This training can cover whatever from basic operation to innovative troubleshooting.
Finally, speaking with solutions supply tactical understandings into enhancing product packaging processes, assisting businesses determine locations for improvement and carry out best methods. On the whole, choosing the appropriate mix of these solutions can dramatically improve packaging procedures.
Trick Features to Try To Find
What important attributes should organizations take into consideration when selecting product packaging devices services? Most importantly, know-how and experience are vital. Providers with a tested record in the sector can offer indispensable insights and options customized to details functional demands. In addition, the availability of comprehensive support services, consisting of installment, upkeep, and troubleshooting, ensures that businesses can depend on timely assistance when issues arise.
One more key feature is the adaptability of solution offerings. A service copyright that can adjust to developing business needs, such as adjustments in production quantity or product packaging specs, will certainly contribute in keeping performance. Modern technology combination need to be a concern; modern packaging tools services need to integrate innovative innovations, such as automation and real-time surveillance, to improve performance.
Lastly, online reputation and customer responses ought to not be forgotten. Engaging with testimonies and case research studies can give a clearer image of a solution provider's dependability and top quality. By considering these necessary characteristics, services can make educated choices that will sustain their product packaging procedures and add to general you can try these out success.
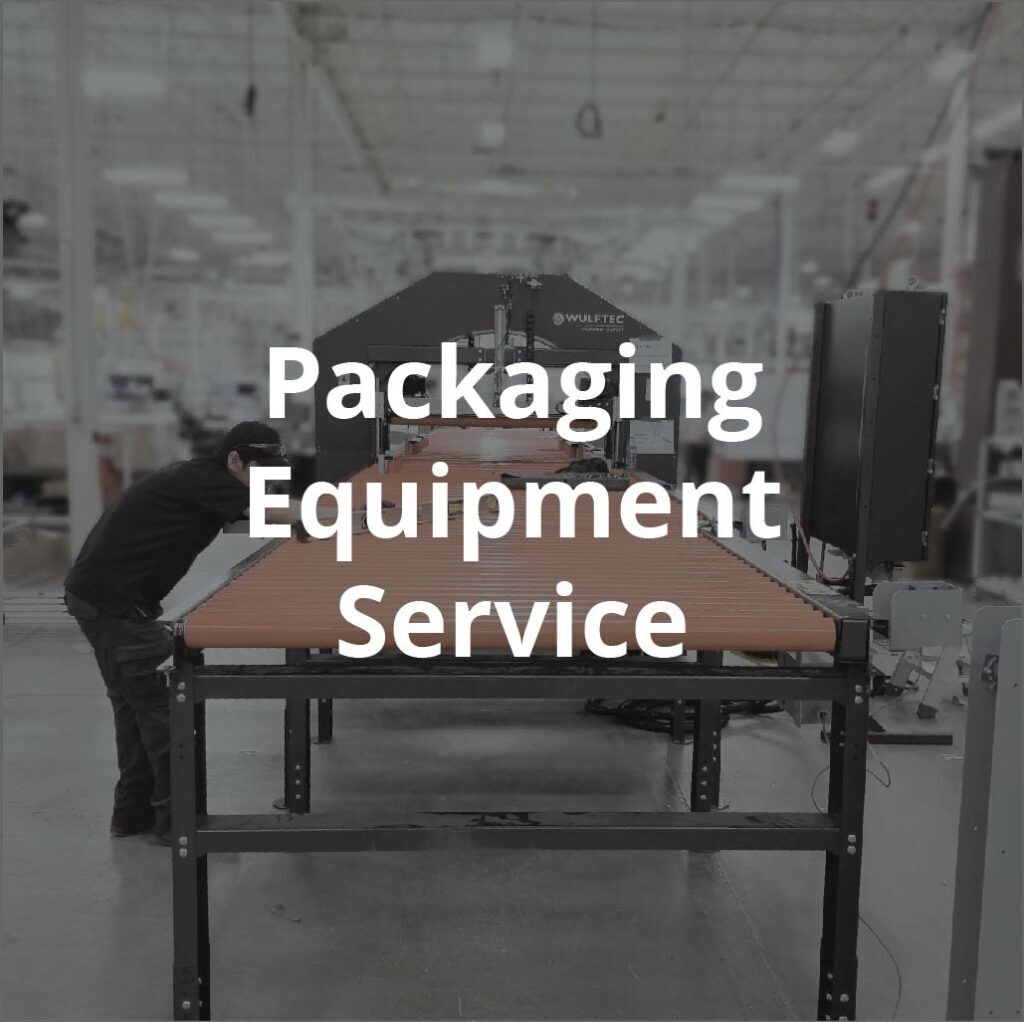
Spending in Long-Term Success
Purchasing long-term success in product packaging tools services needs a strategic technique that focuses on sustainability and scalability. Companies need to concentrate on selecting devices that not just fulfills current operational requirements yet also accommodates future growth and technological innovations. This insight reduces interruptions and boosts total efficiency.
An important part of this financial investment is the regular maintenance and service of devices. Developing an aggressive solution timetable reduces downtime and extends the life expectancy of machinery, eventually causing set you back financial savings. Partnering with experienced provider guarantees that the equipment is enhanced for performance, therefore preserving high production requirements.
Additionally, integrating ingenious technologies, such as automation and IoT connectivity, can considerably enhance operational capabilities. These advancements permit real-time monitoring and data evaluation, making it possible for firms to make educated choices that line up with their long-term goals.
Last but not least, spending in employee training on new innovation and best practices fosters a culture of continuous improvement. By growing an experienced workforce, companies can adjust to altering market demands and maintain their competitive edge. Eventually, an find more info all natural strategy that includes devices, service, modern technology, and workforce development placements business for sustained success in the product packaging market.
Conclusion
To conclude, professional packaging equipment solution plays an essential role in making certain smooth operations within manufacturing environments. The assimilation of precautionary upkeep, fast fixings, and detailed training considerably boosts equipment integrity and decreases downtime. By prioritizing these solutions, companies can attain optimal functional efficiency and prolong the life-span of their machinery. Inevitably, investing in specialist support promotes lasting success, enabling companies to keep high item quality and competition in a developing market landscape.
Report this page